Manufacturing at Bluechips
Our headquarters and factory is based in The Northern Thai city of Chiang Mai. At the heart of our facility is our production floor where we manufacture the products of our growing list of industry-leading customers. As an EMS supplier, the quality of our manufacturing processes is reflected in the products that we ship out on a daily basis. As a result, we have taken great care to make sure that our service meets and exceeds your standards with the following considerations central to our philosophy.
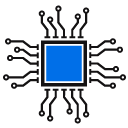
Full-Product Manufacturing
Manufacturing with Bluechips means that you can trust one supplier with the entire production of your goods. Whether it is a small and simple PCB or a complex box-build, our turnkey production service means that we can take care of the process from beginning to end. With major investments in machinery, processes and people, we have established a production floor and service that can efficiently deliver your products and with 20 years of experience in electronic contract manufacturing; we are confident we can become your EMS supplier of choice.
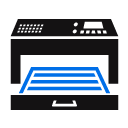
Multiple Production Processes
Modern electronics cannot be produced in any one way so to remain competitive Bluechips has to offer our customers a wide range of processes based on the needs and specifications of your products. As a result, we offer full capabilities on everything from PCB cleaning and inspection to box build assembly and laser marking. Our SMT, COB & soldering capacity means that we can deal with any size, mix or complexity of product with a range of laser marking, powder coating and etching available to personalise your product and ensure you can trust your entire product to just one supplier.
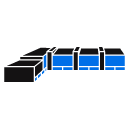
Tailor-Made Production Floor
Like our entire building, the production floor was subject to a long design process intended to optimise everything about the way we work as a company.
As a result, our 2400m2 production floor was designed to allow us to increase our capacity and workforce with further room to grow in the future. With our capacity and ability to work multiple shifts, our production floor can cater to either high mix or high volume production based on the needs of our customer base. While many other companies in manufacturing have built standard facilities in industrial parks, we believe our method of building something unique and effective puts us in a great position to partner dynamic companies and their production needs.
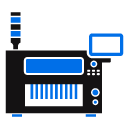
Top-End Machinery
No EMS production floor can be operational without the machinery required to manufacture products for your customer. However, Bluechips prioritises continual investment in the machinery we use to make sure that we produce faster, more efficiently and with consistently high results. Our recent investments in multiple Fuji SMT lines, additional soldering ovens and further AOI, screen printing and laser marking machines highlight our commitment to continuously improve and offer the very best service possible to our growing list of customers.
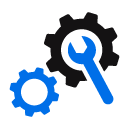
Optimally Engineered Processes
Alongside having the best machinery available, Bluechips has a multi-national team of experts to make sure that our equipment is running at maximum efficiency and without unnecessary downtime. Our Process Engineering team have specific machines and processes that they meticulously take care of so that our customers do not have to worry about avoidable mistakes when they entrust us with their products. Our Business Improvement team work alongside everyone in Production to further ensure that we don't just maintain our effectiveness; we proactively improve it.
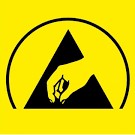
ESD Certified Throughout
Our production floor, warehouse and packing areas are fully ESD certified by ANSI S20.20 and IEC standards. That means that we have taken precautions to avoid any electrostatic discharge at every stage of material handling. All flooring and surfaces are ESD approved with operators grounded at all times when working in production. Production and office staff have to comply with our regulations when entering the production floor and are trained regularly to upkeep our compliance. This certification is another step in our approach to making sure we can offer quality throughout the entire process of working with Bluechips as your trusted contract manufacturer.
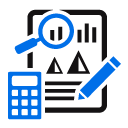
Component Traceability
A key part of our drive for efficient manufacturing is to make sure we leverage all available data to make sure that our consumption, set-up time, changeovers and process flow are all working optimally. Within our ERP system and in-house monitoring program, we can make sure that products are being produced in the manner and timeframe that we can expect. In the unlikely case of any issues, we can react as quickly as possible and make sure that our delivery schedules are not effected. This, plus our team working on ensuring any issues are isolated rather than repeated, allows us to constantly optimise our production processes.
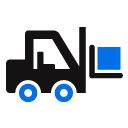
Optimised Material Flow
Another benefit of Bluechips designing our entire facility from scratch was the opportunity to customise every aspect of our material and production flow. Even before your product enters our production floor it is stored in our 600m2 climate-controlled warehouse to keep all the components in the ideal conditions. From there, everything to do with your product will take a natural flow through our production facility from SMT to various stages of quality checks onwards to any final assembly and packing. Simplifying our process flow before production even begins has been an easy but effective step towards perfecting our production procedures.
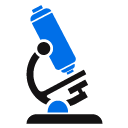
Rigorous Quality Assurance & Testing
While manufacturing and Quality Assurance are different departments within the company, it is impossible to describe our production service without emphasising our attitude towards the quality of our products. Our production floor has testing and inspections available within our SMT and soldering lines to make sure that products do not go from one process to another without being cleared to do so. Everything that is manufactured in our facility is tested to make sure that it meets both the specifications of our customer and the stringent quality guidelines we set internally.