Quality Assurance & Testing at Bluechips
When you partner with a contract manufacturer, you are trusting your supplier with a huge responsibility. We treat your electronics as if they were our own and make the quality of our production the top priority at every stage of working together. When Bluechips was established, it was with the mindset of offering what many companies based in China and other parts of Asia cannot; consistent quality with regards to production, communication and pricing. To make sure this ideal does not fade, we continue to emphasise and invest in our quality processes in the following ways:
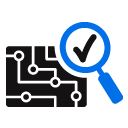
Quality First Philosophy
Bluechips was established with the founding principle of offering cost-effective electronics manufacturing without having to sacrifice quality, communication or reliability. 20 years later, it remains the backbone of our service. Our customer retention has been a key factor in the growth of Bluechips and our approach to high-quality production is one of the main reasons that customers continue to put their trust in Bluechips as their product lines and companies continue to grow.

Specialised Workforce
In order to make sure we produce a high standard of electronics, around 20% of the Bluechips team work directly in either the Quality Assurance or Testing departments. The result of that is a highly trained and determined team who enable us to maintain our quality standards at every stage of our production process; whether it is samples or mass production. Even when faults occur, our team can analyse these and rectify the issues in collaboration with the customer. Our team here at Bluechips also ensure we get the accreditations to highlight our quality standards and target markets.
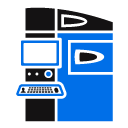
Up-To-Date Machinery
Along with production machinery, Bluechips invests heavily in the latest equipment for testing our products. That includes our x-ray machine, 3D Automatic Optical Inspection as well as equipment to inspect our soldering, PCBs and a range of specific equipment requested by our customers. We are happy to develop and cooperate on machinery and processes based on our discussions with customers. That way, we can detect and prevent problems as early as the design phase of your project.
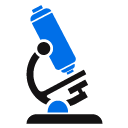
Rigorous IQC
A major aspect of our quality control is making sure we do not limit out standards to the products we send out. It is just as important to make sure the components we order to the company also meet our standards and that of our customers. We have a dedicated Incoming Quality Control team with specific equipment who make sure that our suppliers can consistently meet our expectations so that every level of your supply chain is up to scratch.
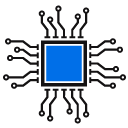
Functional Testing
In order to make sure that we can test the products to the specifications and applications of the customer, we regularly implement functional testing to make sure that the PCBs and turnkey products we manufacture will function correctly. We can do this via test equipment supplied by our customers or we can develop testing requirements and equipment based on your specifications and with the use of LabView soft/hardware.
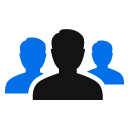
Whole Team Approach
The quality of our products is vitally important to our service and our reputation as an EMS supplier. However, we believe that quality is reflected in every aspect of what we do. The importance we place on quality is emphasised throughout the entire company so that the whole Bluechips team can understand the importance of a satisfied customer. That means that everyone from Customer Service to our engineers highlights the importance of quality and will physically check that processes are being undertaken with care.